New machine concept
EAGLETec
inside
With the EAGLE G5 Precision, we have started in a new era in spark erosion. The die-sinking EDM machine achieves unprecedented precision and surface quality with minimum wear. The fully closed design of the EAGLE G5 Precision, combined with active temperature control, ensures extremely constant thermal stability, which is essential for maximum accuracy and perfect results. Thanks to its encapsulation, the EAGLE G5 Precision is easy to operate manually. The complete automation capability is a guarantee for the long-term economic efficiency of the machine.
Setup EAGLE G5 Precision
Thanks to the EAGLE PowerSPARK generator, the EAGLE G5 Precision achieves a surface finish with graphite that was previously unattainable. Multi-cavity machining is possible with an accuracy of less than 5 µm from cavity to cavity, and with 50% less wear during finishing.
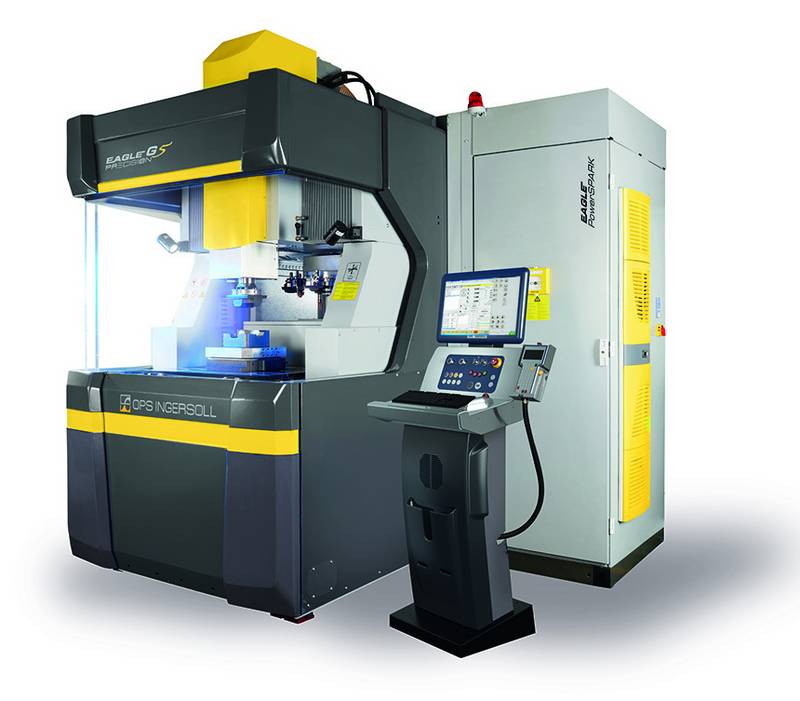
- Maximum precision by increased thermal stability
- Unique fine surfaces with graphite
- Multi-cavity machining with 50% less wear
C = 360°
max. 1.000 kg
Standard configuration
Technical data
Top precision even with copper electrodes
New copper
technology
Not only the graphite technology, but also the copper technology of the EAGLE G5 Precision has been significantly improved. For surfaces below VDI 16 with numerous cavities, the highest precision can be obtained with copper. The new Clean Finish Step provides absolutely homogeneous surfaces - even in 3D geometries.
- Multi-cavity machining below VDI 16
- Minimal wear
- Homogeneous surfaces by Clean Finish Step
Configuration
The sophisticated machine concept of the EAGLE G5 Precision includes a wide range of technical features that ensure extreme accuracy of less than 5 µm on the part. These include constant temperature stability and perfectly coordinated control technology for maximum repeatability.
Precision features




- ADC – Active Dielectric Cooling
- PGC – Position- & Geometric Compensation
- TC – Temperature Compensation
- IPR – Increase Precision & Repeatability
Included in the standard version
- EAGLE PowerSPARK Generator 60 amps
- EAGLE PowerSPARK fine finish package with graphite
- EAGLE PowerJUMP with 18m/min intrval speed in the Z-axis
- Linear measuring system in all axes
- ECOTEC energy saving function
- Precision package with head cooling, spindle nut cooling and work tank temperature control
- Telescopic exhaust unit at the working head
- C-axis
- Electrode changer 20 positions
- Pressure flushing programmable, suction connection manually
- Filter unit, 16m² paper filter
- CO2 fire-extinguishing system
Further options (selection)
- Generator 110 amps
- Technology package for carbide machining
- Special software options for e.g. eroding without dielectric coverage (BA4)
- Electrode and workpiece clamping systems from all well-known manufacturers
- 30 position electrode changer
- Oil mist suction unit
Automation extensions
- MultiChange light/perfomance for the connection of up to 2 machines
- Preparation (interfaces) for third-party automation systems, e.g. EROWA, INDUNORM
- Jobmanagementsoftware, e.g. EVOMECS, CERTA, SOFLEX
With automation into the next generation of precision machining
Our future-oriented automation solutions of the MultiChange handling systems ensure even greater efficiency, thanks to fully automatic and extremely time-saving changing systems for electrodes and workpiece pallets. Another advantage: Our MultiChange systems are able to handle the technology combination of high speed milling and spark erosion, even with several machines.