Precision in a small footprint
EAGLETec
inside
Our smallest model - the GANTRY EAGLE 400 - sets standards in precision mould making in response to the continuously increasing requirements of this industry. This unique product highlight offers maximum precision due to the gantry design, increased efficiency and consistent utilisation of synergy effects in HSC and EDM engineering technology.
Setup GANTRY EAGLE 400
With its compact design and good accessibility, the GANTRY EAGLE 400 is the ideal entry-level model for high-precision die-sinking EDM of small applications. The EAGLE PowerJUMP ensures optimum flushing of the working gap with lifting speeds of up to 18 m/min in the Z-axis.
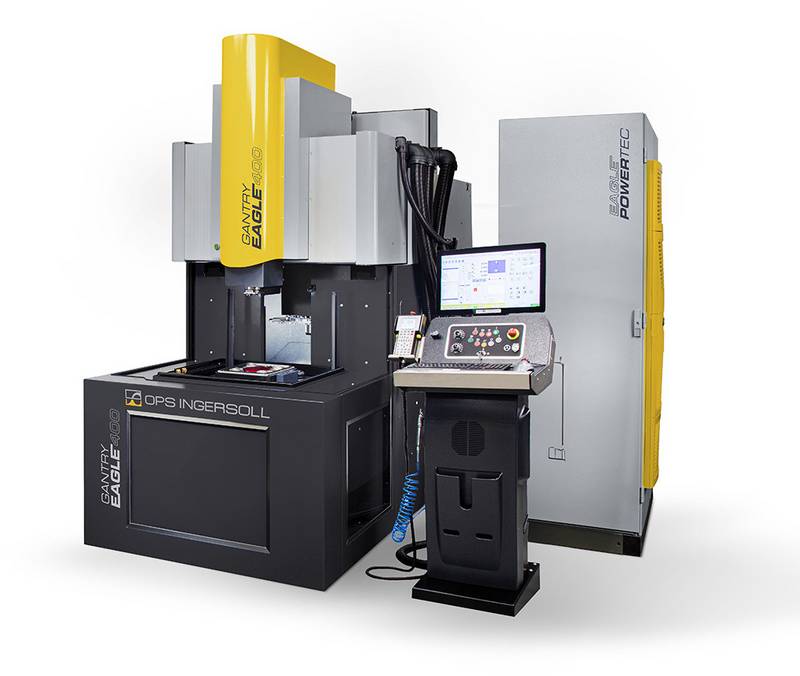
- User-friendly concept
- Optimal accessibility
- Extremely compact
C = 360°
max. 500 kg
Standard configuration
Technical data
programmable/automatic
Configuration
In addition to numerous precision features, our EAGLE G-Line machines can be perfectly equipped to your specific application with optional extensions.
Precision features




- ADC – Active Dielectric Cooling
- PGC – Position- & Geometric Compensation
- TC – Temperature Compensation
- IPR – Increase Precision & Repeatability
Included in the standard version
- EAGLE PowerTEC fine finish generator PT60
- EAGLE PowerJUMP with 18m/min intrval speed in the Z-axis
- Linear measuring system in all axes
- ECOTEC energy saving function
- C-axis
- Electrode changer 20 positions
- Pressure flushing programmable, suction connection manually
- Filter unit, 16m² paper filter
- CO2 fire-extinguishing system
Further options (selection)
- Generator 110 amps
- Technology package for fine finish and carbide machining
- Special software options for e.g. eroding without dielectric coverage (BA4)
- Electrode and workpiece clamping systems from all well-known manufacturers
- 30 position electrode changer
- Oil mist suction unit
Automation extensions
- MultiChange light/perfomance for the connection of up to 2 machines
- Preparation (interfaces) for third-party automation systems, e.g. EROWA, INDUNORM
- Jobmanagementsoftware, e.g. EVOMECS, CERTA, SOFLEX
With automation into the next generation of precision machining
Our future-oriented automation solutions of the MultiChange handling systems ensure even greater efficiency, thanks to fully automatic and extremely time-saving changing systems for electrodes and workpiece pallets. Another advantage: Our MultiChange systems are able to handle the technology combination of high speed milling and spark erosion, even with several machines.